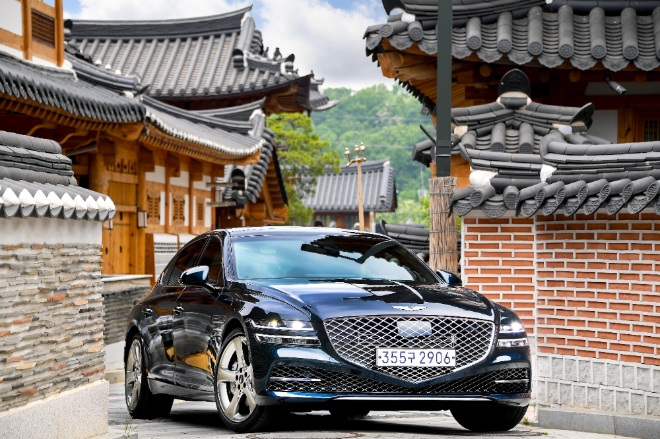
특히 전기 자동차의 등장은 자동차 업체에게 내연기관 시대와는 또 다른 소음을 잡아야 하는 과제를 던져주었다. 더 정숙한 자동차를 위한 소음 저감 기술 개발이 치열하게 전개되고 있다.
가장 현실적인 방법은 ‘음향재료 사용’
공기 및 구조 전달 소음을 저감하기 위해 자동차 업체들은 ▲소음흡수 및 반사 음향재료 사용(다공성 흡음 재료, 고밀도 시트) ▲구조변경(강성 증대, 진동 모드 변경) ▲진동절연 또는 흡수재료 사용(점탄성 재료, 스프링) ▲능동 소음 제어(소음과 반대 위상 음파 발생으로 상쇄) 등 4가지 방법을 주로 활용하는데, 모든 자동차에 공통적으로 적용하는 방법은 ‘음향재료의 사용’이다.
흡차음 기술의 핵심은 음향재료에 있다. 운전자에게 보이지는 않지만, 우리가 사용하는 자동차 곳곳에 흡차음 부품을 적용했다. 다공성 음향 재료로 제조되는 흡차음재는 다양한 종류로 구성돼 있는데, 최근에는 환경 문제와 비용 효율, 성능 등을 고려해 페트(PET) 부직포, 초극세사, 우레탄폼 등이 주로 사용되고 있다. 차랑 한 대당 약 20kg 내외의 음향재료가 사용되고 있으니, 결코 적은 양은 아니다.
전기차, 수소전기차 등 친환경차로의 전환이 활발히 이뤄지면서 소음 저감 시 고려할 소음원도 크게 달라지고 있다. 내연기관 차량은 엔진 소음이 상대적으로 크게 실내로 유입되었으나, 엔진이 사라진 전기차에서는 노면 소음과 바람 소리가 주요 소음원으로 여겨지고 있다. 또한, 전기차의 고출력 모터에서 발생하는 고주파 소음이 새로운 소음원으로 지목되고 있고, 넓은 실내공간을 확보하기 위해 음향재료의 투입 공간이 줄어드는 경향도 보이고 있다.
소음 줄이려면 많이, 실내공간 늘리려면 적게 사용 딜레마
먼저, ‘PET 섬유’는 자동차 음향재료로 가장 많이 사용되고 있지만 정숙성을 높이고 재료 사용량을 줄이기 위해 고효율‧고성능 PET 섬유가 필요로 한다. 현대차는 매끄럽던 PET 섬유 단면을 톱니바퀴 형태로 설계해 음파와의 마찰 효율을 끌어올리는 표면을 형성해 본 결과 기존 섬유 대비 10% 이상 흡음률이 개선됐다. 특히 이형도(형상이 원형에서 얼마나 멀어지는지를 나타내는 수치)가 가장 높은 8엽형은 20% 이상의 흡음률 개선 결과를 나타냈다..
‘폴리우레탄(polyurethane) 폼’은 적은 중량 대비 우수한 흡음 성능을 갖고 있다. 셀이라는 독특한 미세구조로 되어있기 때문이다. 폴리우레탄 폼의 발포 과정 중 미세입자인 탄소나노튜브(CNT)를 첨가해 셀의 기하구조를 변경해 테스트 해 본 결과, 주파수 800kHz 이하인 저주파 대역은 미세구조의 영향을 덜 받고, 이상인 고주파 대역은 영향을 많이 받으며, CNT를 0.3% 이상 첨가하면 흡음률에 영향을 미친다는 것을 확인했다. 이러한 과정을 통해 차량의 정숙성을 높일 수 있는 최적의 우레탄 폼 기하구조를 만들 수 있는 방법을 찾아냈다.
‘멜트 블로운(Melt-Blown) 섬유’는 PET 섬유 대비 중량이 가볍고, 흡음 성능은 매우 우수한 극세사 섬유재료다. 멜트 블로운 섬유 극세사를 기존 대비 50% 축소해 음파와 마찰할 수 있는 섬유의 개체수를 증가시키고, 불규칙한 섬유 구조체를 섞었더니, 섬유가 얇아질수록 흡음률이 향상됐다.
G80‧K9‧아이오닉6에 적용, 우수한 소음 저감 효과 거둬
기아 K9은 CNT 복합 폴리우레탄 폼을 적용해 흡음률을 0.7 이상으로 높였다. 기존 흡음재와 글래스울과 레진펠트 등이 0.7에 못 미치는 것과 비교해 우수한 흡음률을 기록했다.
현대차 아이오닉5에는 초극세사 멜트 블로운 섬유를 적용, 흡음율을 0.8 이상을 기록, 기존제품 0.6, 수입제품 0.7보다 한 단게 더 높은 성능을 보여줬다.
이 책임연구원은 “차량의 실내 소음은 다양한 원인으로 발생하고 있다. 특히, 전기차의 등장으로 과거와는 다른 소음 환경에 직면했으며, 이를 해결해야 한다”면서, “이를 줄이기 위해 다각도로 연구를 진행해 진보한 소음 제어 기술을 개발하여 더 나은 주행 경험을 제공할 것”이라고 말했다.
채명석 글로벌이코노믹 기자 oricms@g-enews.com